Under Slab Piping
Our Brochures
For More Information
You can also send us an email and we’ll get in touch shortly, or You Can Call Us: 855-937-6945
Under Slab Piping.
Class A VA Contractor License #2705147099
DMBE VA SWAM # 684641
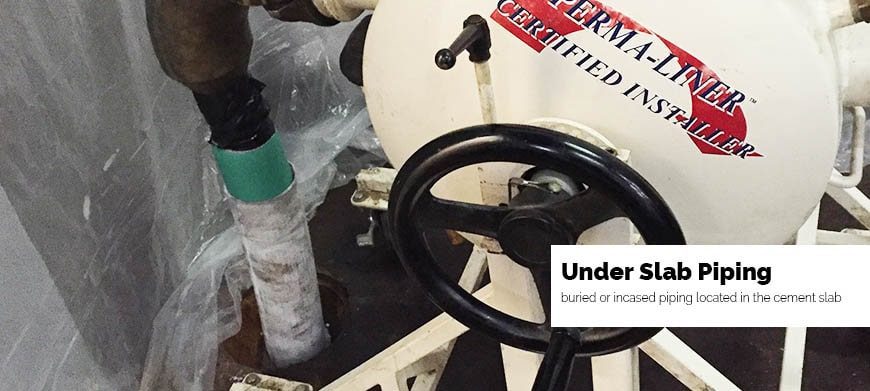
What is under slab piping?
Under slab piping refers to the buried or incased piping located in the cement slab of a building or facility. This piping is complex in nature, having many different piping segments serving a variety of plumbing fixtures that intersect together as all effluent makes it way downstream. The diameter of slab piping segments can change unexpectedly and make several different bends ranging from 22 degrees to 90 degrees. Under slab piping has been known to be made of a variety of materials including but not limited to: cast iron, ductile iron, and PVC.
What happens over time to under slab piping?
Much like other building or facility assets, under slab piping ages and the material surface becomes thinner and rougher overtime. Metallic based slab piping such as cast iron, which is the most common under slab pipe material, can be vulnerable to surface corrosion from years of chemical and detergent use. As chemical corrosion matures the pipe surface thins and begins to form linear and longitudinal cracks. More aggressive surface corrosion can lead to what we call bottom channeling. Bottom channeling occurs when heavy levels of corrosive effluents erode a cavity or channel in the bottom of the cast iron slab piping overtime. In some cases, up to 30-50 percent of the piping can be totally gone!
What is Dynamic Drain Technologies process for lining under slab pipe?
At Dynamic Drain Technologies, we use a design first philosophy. Due to the complex nature of under slab piping it is vital that we understand and observe all construction, operational and structural details of a buildings slab plumbing system.
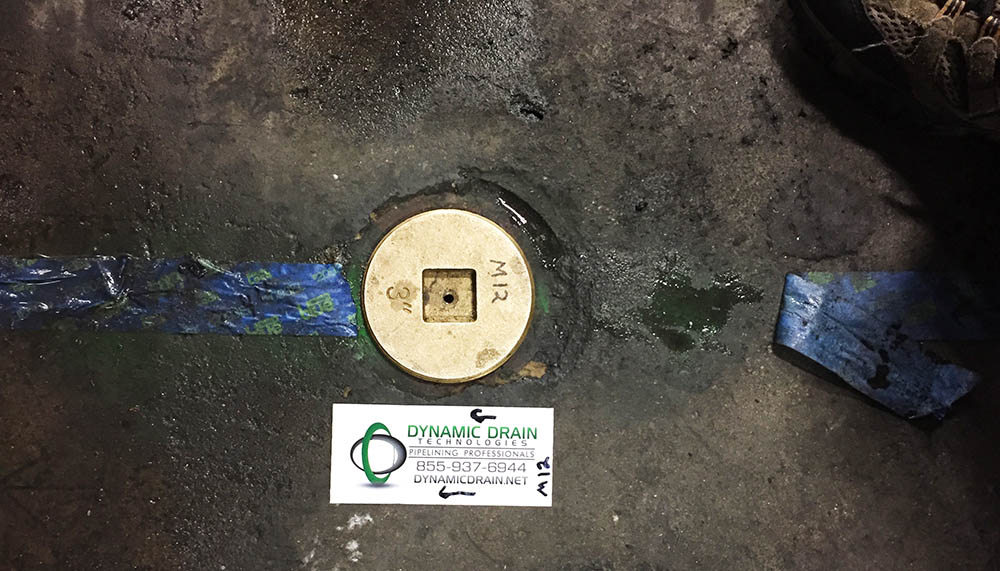
The design process starts with a site survey in which all plumbing and drain fixtures are accounted for. Our team of specialists then tag and title the access points such as cleanouts, manholes, or toilet closet bends. These access points provide entry to the under-slab piping system. Access is vital and must be considered when moving forward into the video inspection and pipe cleaning phases.
Pipe Inspection and Location.
Pipe inspections allow us to do several very important things. First and foremost, they allow us to locate and map the piping system. We can see the plumbing and drain fixtures above the ground but we need to understand how and where they intersect underground. We trace the slab piping system via a sonde transmitter located in our camera heads. We often place painters tape on the slab surface to mark the location and depths of the under-slab piping. Digital site plans are also generated during this process. Pipe inspections also allow us to gather and observe conditional data points of the slab piping system. This data consists of structural, operational, and maintenance related observations that determine the proper methods and levels of pipe cleaning and preparation needed to install a cured in place slab pipe liner.
Design
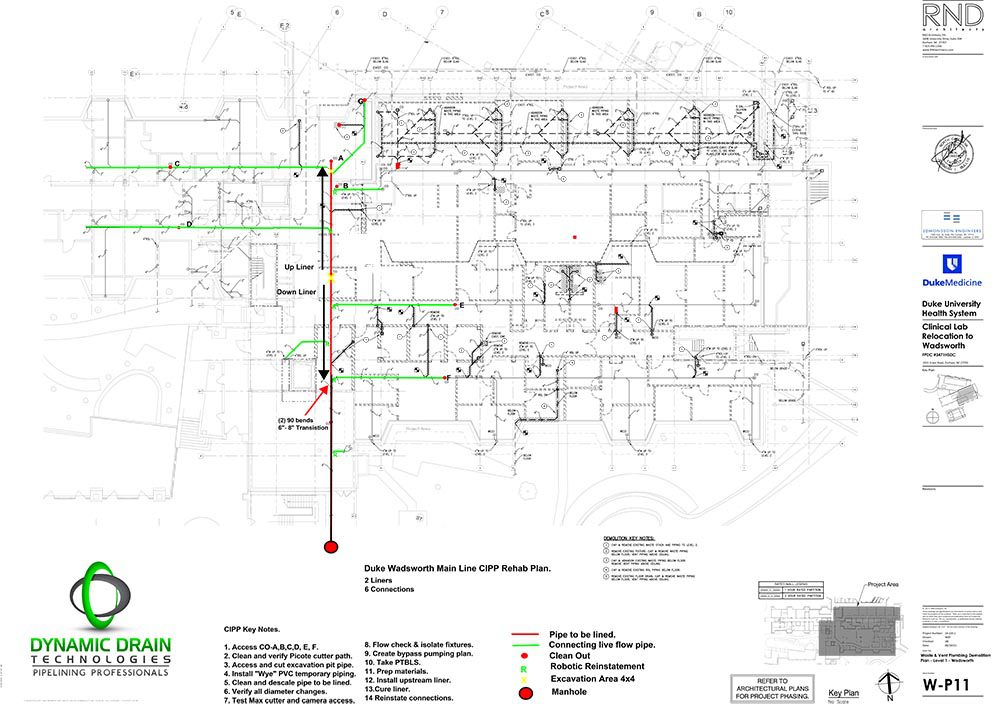
At this point we have all the information needed to present the data and layout the action or pipe lining design. Design will cover the following areas: scope of works, approximate pricing, working hours, project durations, pipe cleaning, diversion or bypass pumping options, CIPP liner design calculations, and finally project management requirements and responsibilities.
Detailed Pipe Inspection Reports
Pipe Cleaning
The pipe cleaning process requires a remarkable amount of labor and technical expertise. A typical under slab pipe cleaning scenario may call for heavy amounts of mechanical chain knocking or scouring of the internal pipe surface. This process removes years of rust deposits from the pipe walls and surfaces. The dislodged debris are then washed out with forced air or high pressure water jetting. The desired result of this process is to achieve a clean pipe surface, free of any deposits or roughness that could interfere or interrupt the bonding of the cured in place pipe liner.
Cured in Place Pipe Lining of Under Slab Piping.
Once the pipe is completely cleaned, technicians then perform another video pipe inspection to record the pipeline before the pipe liner is installed. This is done to show that the pipe was properly prepped and cleaned prior to installing the liner. All lining materials are fabricated onsite using our turnkey job-ready mobile trailer units. Our mobile lining trailers are outfitted with state-of-the-art electric vacuum assisted wet out tables. The liner material is loaded onto the roller table and the epoxy resin is introduced to the liner and passed through the electric roller until the liner has reached 100 percent saturation.
Now the liner is ready to be loaded into one of our inversion devices and inverted into the pipeline using compressed air. This process is called inversion. For single access installations, a bladder or calibration tube is inserted after the liner and inflated to press the liner against the pipe walls. Once inversion is complete a curing method is implemented. Depending on the application the liner can be cured in 3 different ways. The most time-consuming method is an ambient cure. During an ambient cure epoxy resins are combined with an accelerator that will encourage a natural air cure within 3-4 hours of installation. Faster cure times can be achieved by using external heat sources. The quickest external heat source is steam. Forced steam is passed through the liner until the epoxy reaches its desired exothermic flash point. The same outcome can also be achieved by filling the inverted liner with water and recirculating it through a boiler. Depending on the diameter and length, using steam or boiling water can reduce cure times to 1-2 hours.
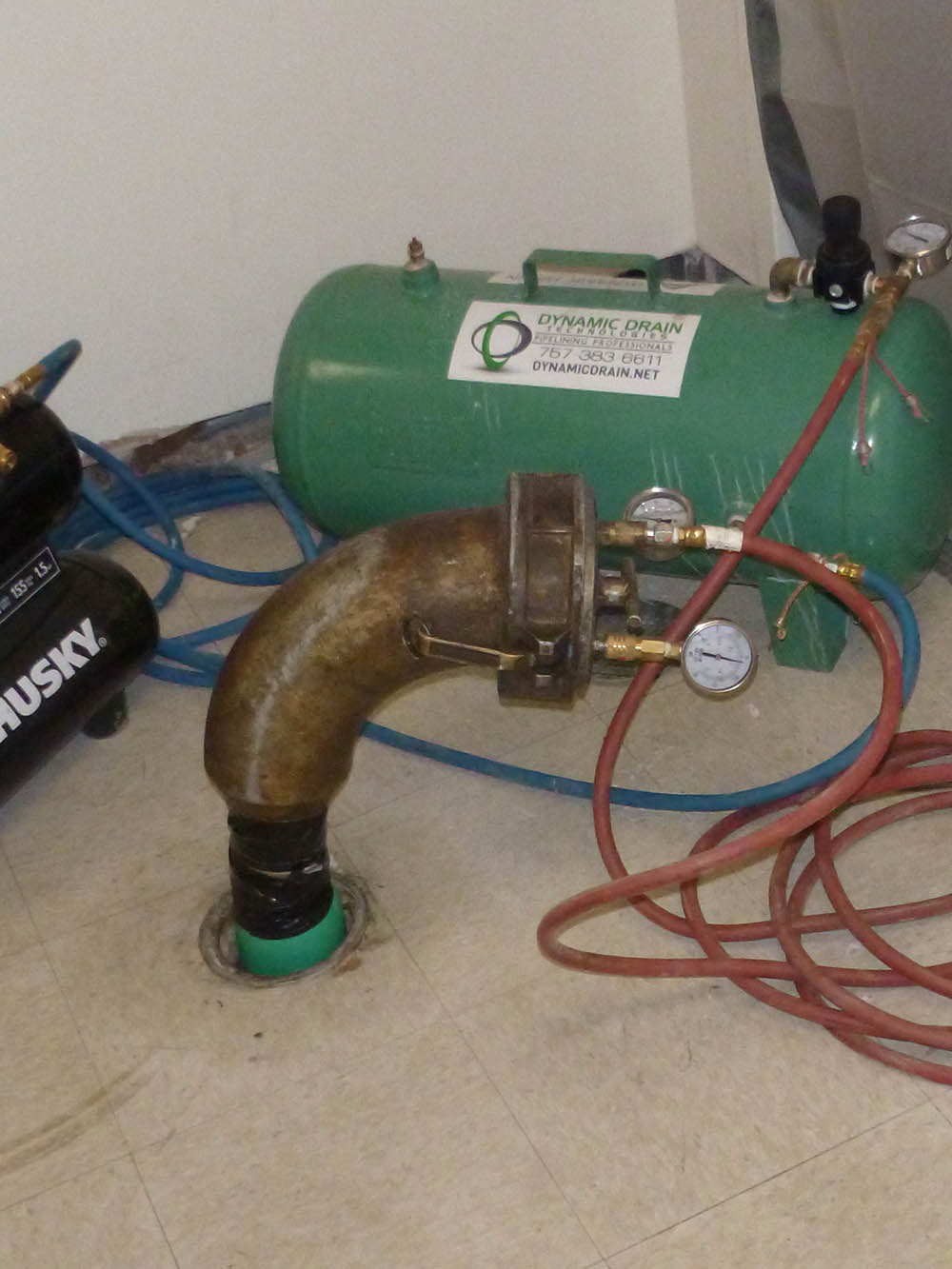
After a proper cure time is reached, air pressure can be released and the calibration tube can be removed. At this point the liner is now fully cured and bonded to existing pipe walls. A post liner video inspection is then conducted verifying the quality of the install. Then, especially in an under-slab pipe environment, it will be necessary to reestablish or reinstate the cross connecting service pipes that our liner has covered. This is done by placing a robotic and pneumatic driven cutter into the pipe liner and grinding out the connections while monitoring with a video inspection camera. After all connections, have been reestablished, the pipe liner is then flushed again with high pressure water to remove all debris from the reinstatement phase. A final pipe inspection video is produced to show the newly installed and reinstated slab piping.
At the finale of our process we have achieved an internal pipe repair without the need of excavation. This pipe liner will have 50-year design life and will improve flow capacity by as much as 75%. Slab pipe lining is one of the most cost-effective pipe repair options a facility will encounter. Downtime can be limited or possibly eliminated by using this trenchless technology.