Main Line Sanitary & Storm Sewers
Our Brochures
For More Information
You can also send us an email and we’ll get in touch shortly, or You Can Call Us: 855-937-6945
Main Line Sanitary & Storm Sewers.
Class A VA Contractor License #2705147099
DMBE VA SWAM # 684641
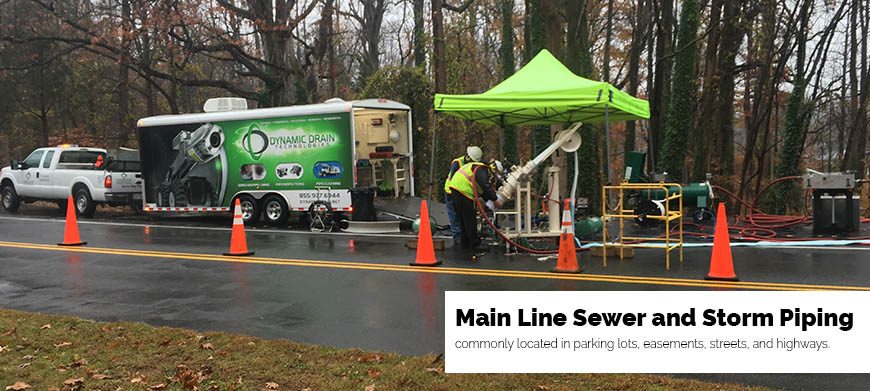
What is Main Line Piping?
Main line sewer or storm pipelines are most commonly located in parking lots, easements, streets, and highways. Some main line piping can also be located off easement in wooded or hard to reach areas. Main line piping infrastructure is responsible for carrying heavy loads of effluent from multiple different facilities or residential structures. This type of piping, also referred to as manhole to manhole pipe, is generally at least six inches in diameter but can increase in size all the way to 54+ inches. Main line piping usually has two access structures on each end and often runs in a straight line. Common structures include: manholes, catch basins, and vaults. The materials used for main line piping are diverse and can be variable based on geographical locations. Conventional main line pipe materials are: Terra Cotta, Vitrified Clay, Unreinforced Concrete, Reinforced Concrete, Asbestos, Corrugated Galvanized, Cast Iron, Ductile Iron, and PVC. Typically, main line pipes are buried at any depth from three feet to over twenty-five feet.
Most main line sewer and storm piping is owned by the local or state governments. As with most American civil infrastructure it has been largely ignored and is nearing or has exceeded is useful design life. Common main line piping defects are: root infiltration, cracking, fracturing, offsets, sags, intruding joint seals, intruding taps, holes, infiltration, and in some cases an entire jointed section can be collapsed. Main line pipe problems can cause: sink holes, water service disruptions, road shutdowns, excessive flooding, pollution, and contamination of local water ways. Over the years the Department of Environmental Protection and the Environmental Protection Agency have levied fines and placed certain municipal governments under what is referred to as a “consent decree”. This consent decree requires local governments to have a multi year evaluation and repair plan on all civil underground piping infrastructure.
What is the process that Dynamic Drain Technologies uses for lining main line piping?
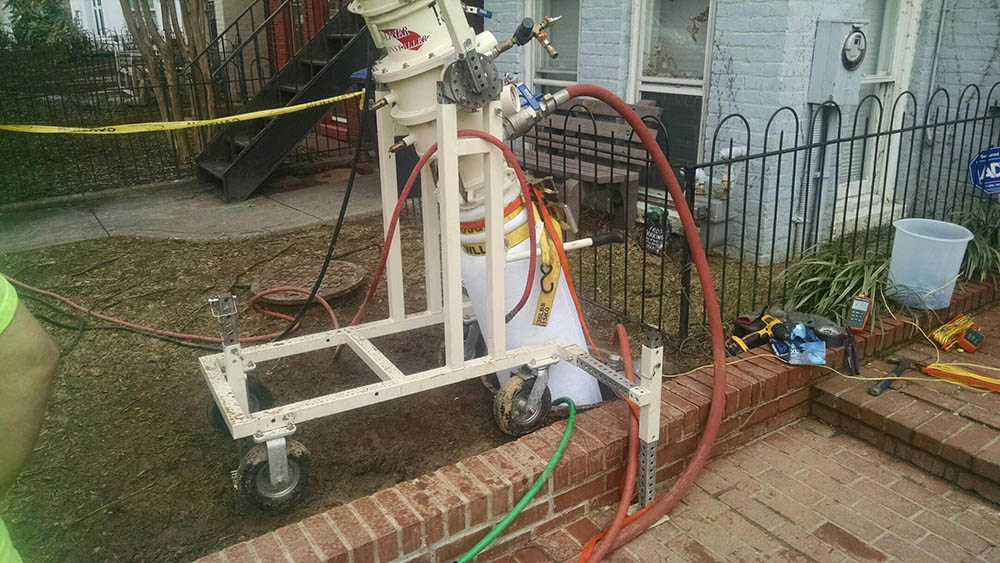
Dynamic Drain Technologies is not currently a major player in the municipal pipe lining industry. We focus on the private infrastructure markets with the exception of higher education institutions, federal campuses, and military bases. In addition to theses clients we also evaluate and use trenchless pipelining technologies for a number of private commercial and multi family infrastructure owners. We have a unique process that closely mimics the guidelines and procedures that major municipal governments use to evaluate and repair mainline sewer and storm piping assets.
Pipe Inspection and Location.
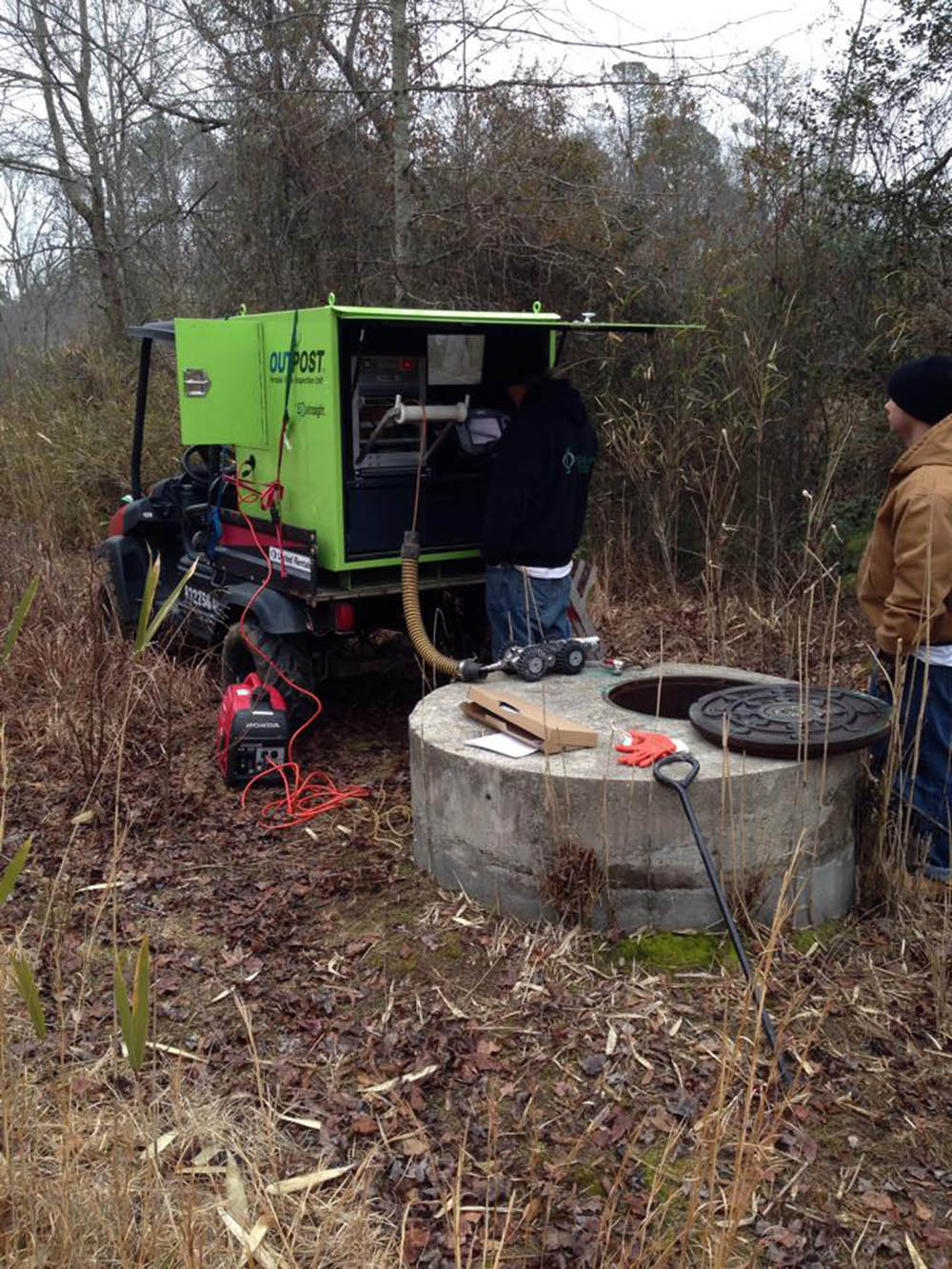
Pipe inspections allow us to achieve several very important things. First and foremost, they allow us to locate and map the piping system. We trace the main line piping system via a sonde transmitter located in our crawling cameras. Spray paint and marking tape are used to sketch the path of the underground pipe system to show infrastructure owners where these main line pipe systems run. Digital site plans are also generated during this process. Additionally, pipe inspections enable our technicians to gather and observe conditional data points of the piping system. This data consists of structural, operational, and maintenance related observations that determine the proper methods and levels of pipe cleaning and preparation needed to install a cured in place pipe liner.
Design
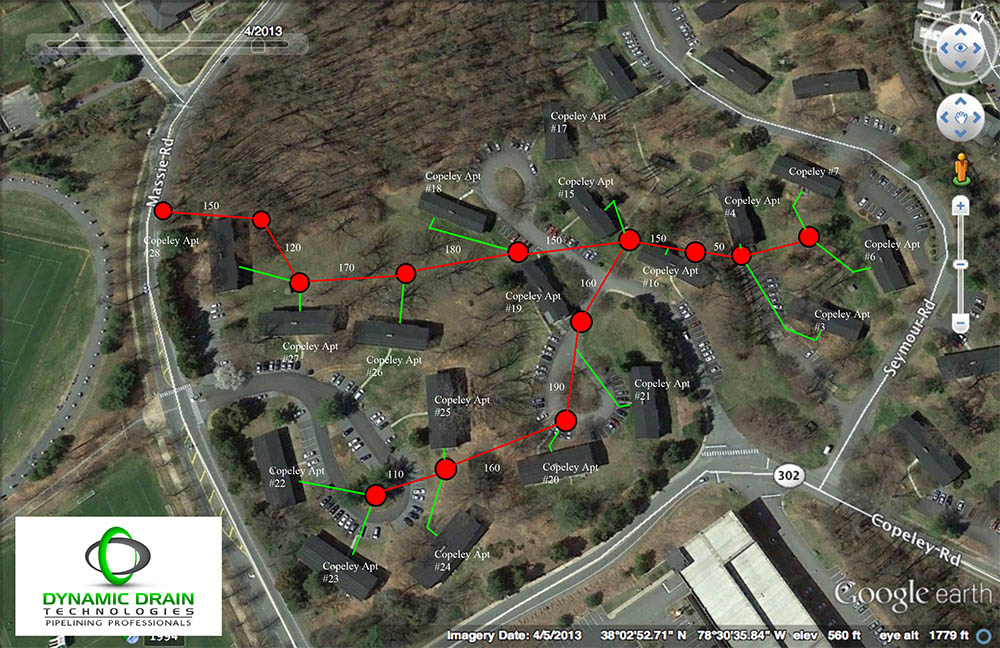
At this point we have all the information needed to present the data and layout the action or pipe lining design. Design will cover the following areas: scope of works, approximate pricing, working hours, project durations, pipe cleaning, diversion or bypass pumping options, CIPP liner design calculations, and finally project management requirements and responsibilities.
Pipe Cleaning
The pipe cleaning process requires a remarkable amount of labor and technical expertise. A typical pipe cleaning scenario may call for heavy amounts of hydro driven chain knocking or scouring of the internal pipe surface. This process removes years of deposits from the pipe walls and surfaces. The dislodged debris are then washed out with high pressure water jetting. The desired result of this process is to achieve a clean pipe surface, free of any deposits or roughness that could interfere or interrupt the bonding of the cured in place pipe liner.
Cured in Place Pipe Lining of Main Line Piping.
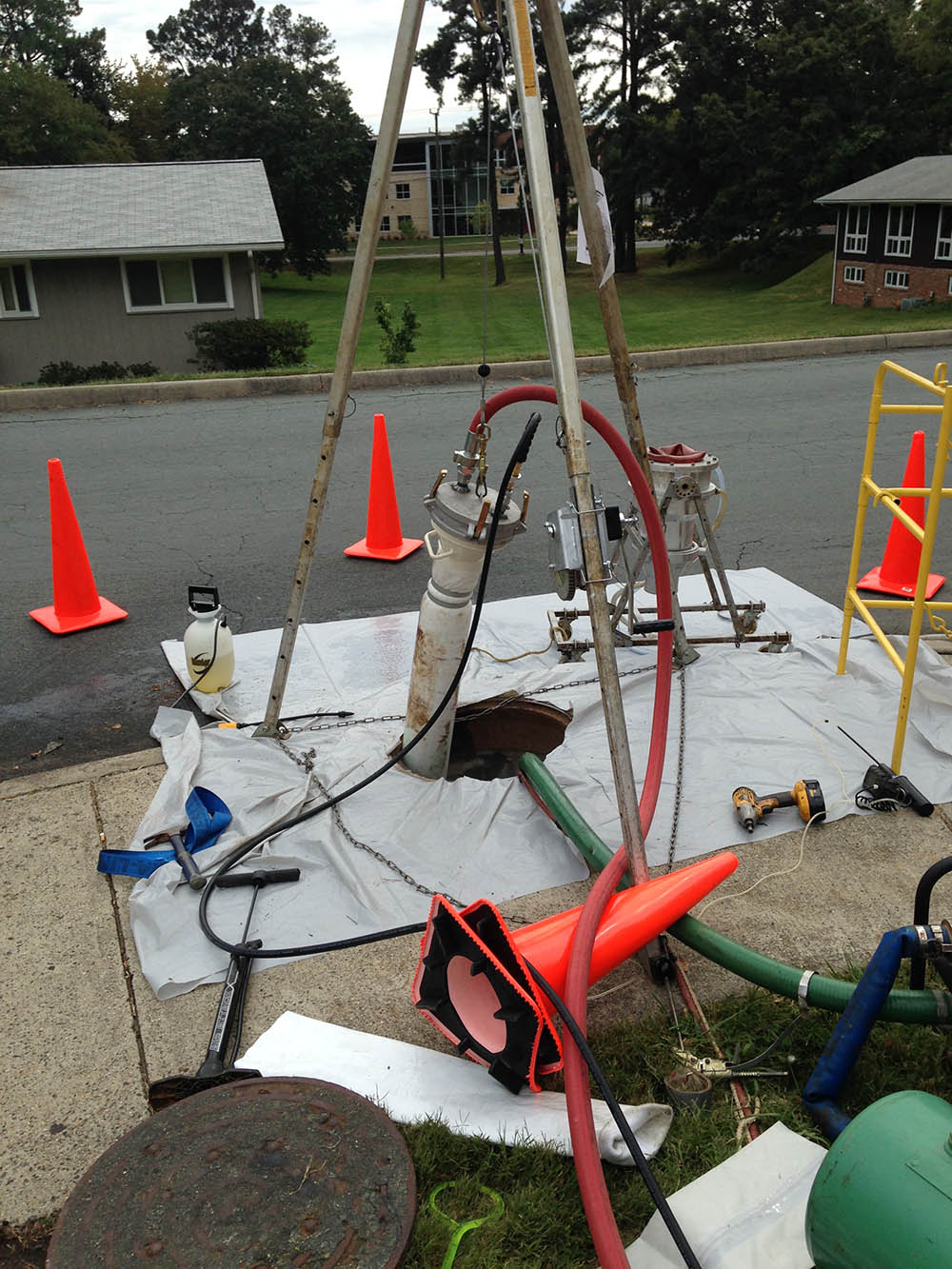
Once the pipe is completely cleaned, technicians then perform another video pipe inspection to record the pipeline before the pipe liner is installed. This is done to show that the pipe was properly prepped and cleaned prior to installing the liner. All lining materials are fabricated onsite using our turnkey job-ready mobile trailer units. Our mobile lining trailers are outfitted with state-of-the-art electric vacuum assisted wet out tables. The liner material is loaded onto the roller table and the epoxy resin is introduced to the liner and passed through the electric roller until the liner has reached 100 percent saturation. For larger jobs, all liners are assembled and wet out a pre determined wet out facility and transported to the job via refrigeration trucks.
Now the liner is ready to be loaded into one of our inversion devices and inverted into the pipeline using compressed air. This process is called inversion. For single access installations, a bladder or calibration tube is inserted after the liner and inflated to press the liner against the pipe walls. Once inversion is complete a curing method is implemented. Depending on the application the liner can be cured in 3 different ways. The most time-consuming method is an ambient cure. During an ambient cure epoxy resins are combined with an accelerator that will encourage a natural air cure within 3-4 hours of installation. Faster cure times can be achieved by using external heat sources. The quickest external heat source is steam. Forced steam is passed through the liner until the epoxy reaches its desired exothermic flash point. The same outcome can also be achieved by filling the inverted liner with water and recirculating it through a boiler. Depending on the diameter and length, using steam or boiling water can reduce cure times to 1-2 hours.
After a proper cure time is reached, air pressure can be released and the ends of the liner can be trimmed. The liner is now fully cured and bonded to existing pipe walls. A post liner video inspection is conducted to verify the quality of the install. Then, especially in main line piping environments, it is necessary to reestablish or reinstate the cross connecting service laterals that our liner has covered. This is done by placing a robotic and pneumatic driven cutter into the pipe liner and grinding out the connections while monitoring with a video inspection camera. After all connections have been reestablished, the pipe liner is flushed again with high pressure water to remove all debris from the reinstatement phase. A final pipe inspection video is produced to show the newly installed and reinstated main line piping.
At the finale of our process we have achieved an internal pipe repair without the need of excavation. This pipe liner will have 50-year design life and will improve flow capacity by as much as 75%. Main line pipe lining is one of the most cost effective pipe repair options an infrastructure owner will encounter. Heavy demolition and downtime can be avoided completely.