Lateral Sewer & Storm Piping
Our Brochures
For More Information
You can also send us an email and we’ll get in touch shortly, or You Can Call Us: 855-937-6945
Lateral Sewer & Storm Piping.
Class A VA Contractor License #2705147099
DMBE VA SWAM # 684641
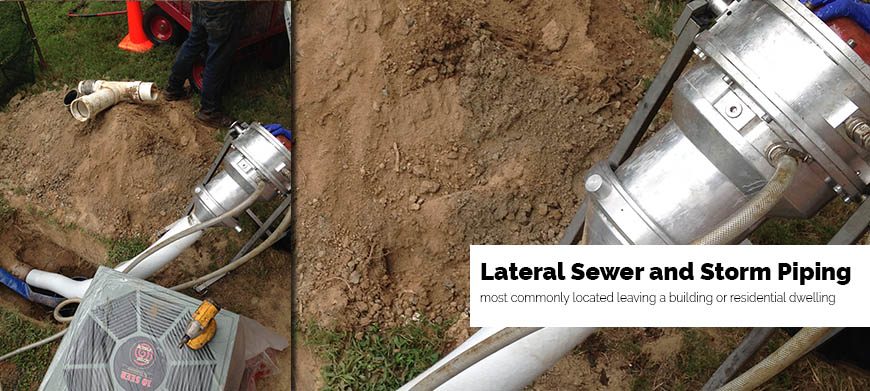
What is Lateral Piping?
Lateral sewer or storm pipelines are most commonly located leaving a building or residential dwelling. Lateral piping extends through easements, roads, and highways where it connects to a larger main line pipe. Lateral piping infrastructure is responsible for carrying effluent from facilities or residential structures to the main line piping. This type of piping is generally at least four inches in diameter but can increase in size all the way to twelve inches or more, depending on facility size and fixture quantity. Lateral piping usually has cleanout access and often runs in a semi straight line. The materials used for lateral piping are diverse and can be variable based on geographical locations. Conventional lateral pipe materials are: Terra Cotta, Vitrified Clay, Unreinforced Concrete, Reinforced Concrete, Asbestos, Cast Iron, Ductile Iron, and PVC. Typically, lateral line pipes are buried at any depth from three feet to over fifteen feet or more.
What happens to Lateral Piping over time?
Most lateral line sewer and storm piping are privately owned. As with most American civil infrastructure, it has been largely ignored and is nearing or has exceeded is useful design life. Common lateral line piping defects are: root infiltration, cracking, fracturing, offsets, sags, intruding joint seals, intruding taps, holes, infiltration, and in some cases an entire jointed section can be collapsed. Lateral line pipe problems can cause: sinkholes, water service disruptions, excessive flooding, property damage, pollution, and contamination of local waterways.
What is the process that Dynamic Drain Technologies uses for lining lateral piping?
Lateral pipe lining is widely becoming a main stream pipe repair strategy. Laterals are generally straight forward and do not require the heavy design process that other more complex piping infrastructure require. Lateral pipelines are highly important. Facilities depends on their functionality to effectively drain the buildings entire sewer or storm effluent. Thus, it is highly important to conduct pre lining video inspections and light cleaning to guarantee the lateral pipe line is a suitable candidate for the cured in place pipelining. This process takes less than a day and is usually less than 5% of the total CIPP repair cost.
Pipe Inspection & Location
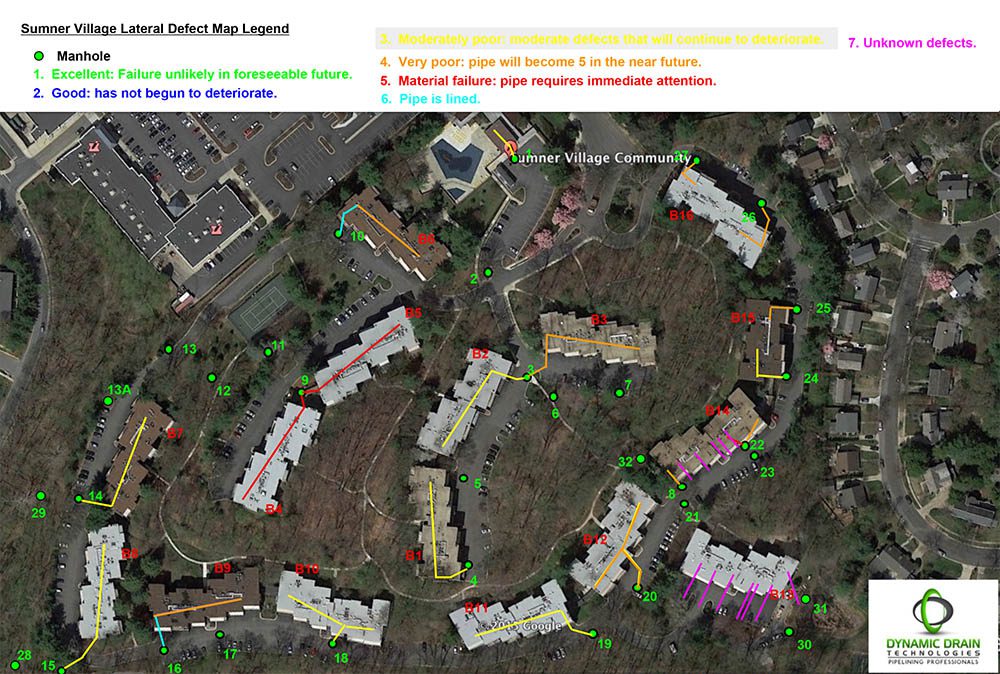
Pipe inspections allow for the achievement of several very important things. First and foremost, they allow us to locate and map the lateral. We trace the lateral piping via a sonde transmitter located in our push cameras. Spray paint and marking tape are used to sketch the path of the underground lateral to show infrastructure owners where the lateral piping runs. Digital site plans are also generated during this process. Additionally, pipe inspections enable our technicians to gather and observe conditional data points of the piping system. This data consists of structural, operational, and maintenance related observations that determine the proper methods and levels of pipe cleaning and preparation needed to install a cured in place pipe liner.
Pipe Cleaning
Pipe inspections allow us to do several very important things. First and foremost, they allow us to locate and map the piping system. We can see the plumbing and drain fixtures above the ground but we need to understand how and where they intersect underground. We trace the slab piping system via a sonde transmitter located in our camera heads. We often place painters tape on the slab surface to mark the location and depths of the under-slab piping. Digital site plans are also generated during this process. Pipe inspections also allow us to gather and observe conditional data points of the slab piping system. This data consists of structural, operational, and maintenance related observations that determine the proper methods and levels of pipe cleaning and preparation needed to install a cured in place slab pipe liner.
Cured in Place Pipe Lining of Lateral Piping.
Once the pipe is completely cleaned, technicians then perform another video pipe inspection to record the pipeline before the pipe liner is installed. This is done to show that the pipe was properly prepped and cleaned prior to installing the liner. All lining materials are fabricated onsite using our turnkey job-ready mobile trailer units. Our mobile lining trailers are outfitted with state-of-the-art electric vacuum assisted wet out tables. The liner material is loaded onto the roller table and the epoxy resin is introduced to the liner and passed through the electric roller until the liner has reached 100 percent saturation.
Now the liner is ready to be loaded into one of our inversion devices and inverted into the pipeline using compressed air. This process is called inversion. For single access installations, a bladder or calibration tube is inserted after the liner and inflated to press the liner against the pipe walls. Once inversion is complete a curing method is implemented. Depending on the application the liner can be cured in 3 different ways. The most time-consuming method is an ambient cure. During an ambient cure epoxy resins are combined with an accelerator that will encourage a natural air cure within 3-4 hours of installation. Faster cure times can be achieved by using external heat sources. The quickest external heat source is steam. Forced steam is passed through the liner until the epoxy reaches its desired exothermic flash point. The same outcome can also be achieved by filling the inverted liner with water and recirculating it through a boiler. Depending on the diameter and length, using steam or boiling water can reduce cure times to 1-2 hours.
After a proper cure time is reached, air pressure can be released and the ends of the liner can be trimmed. The liner is now fully cured and bonded to existing pipe walls. A post liner video inspection is conducted to verify the quality of the install. In some cases, it might be necessary to reestablish or reinstate a cross connecting pipe service or cleanout that our liner has covered. This is done by placing a robotic and pneumatic driven cutter into the pipe liner and grinding out the connections while monitoring with a video inspection camera. After all connections have been reestablished, the pipe liner is flushed again with high pressure water to remove all debris from the reinstatement phase. A final pipe inspection video is produced to show the newly installed and reinstated lateral piping.
At the finale of our process, we have achieved an internal pipe repair without the need of extensive excavation. This pipe liner will have 50-year design life and will improve flow capacity by as much as 50%. Lateral pipe lining is one of the most cost-effective pipe repair options a building owner or manager will encounter. Heavy demolition and downtime can be avoided completely.
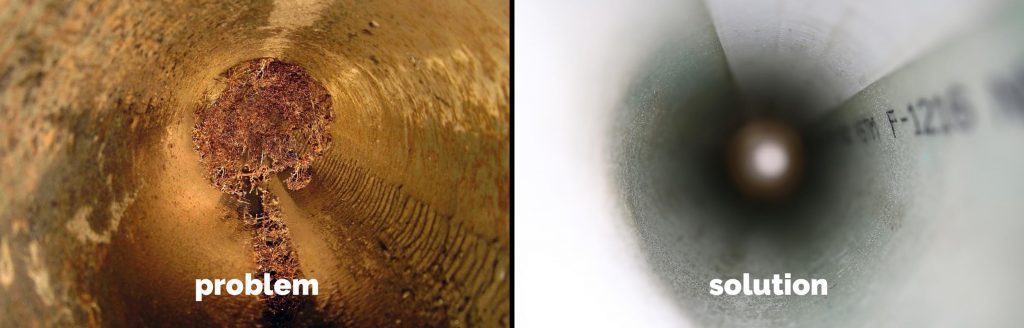